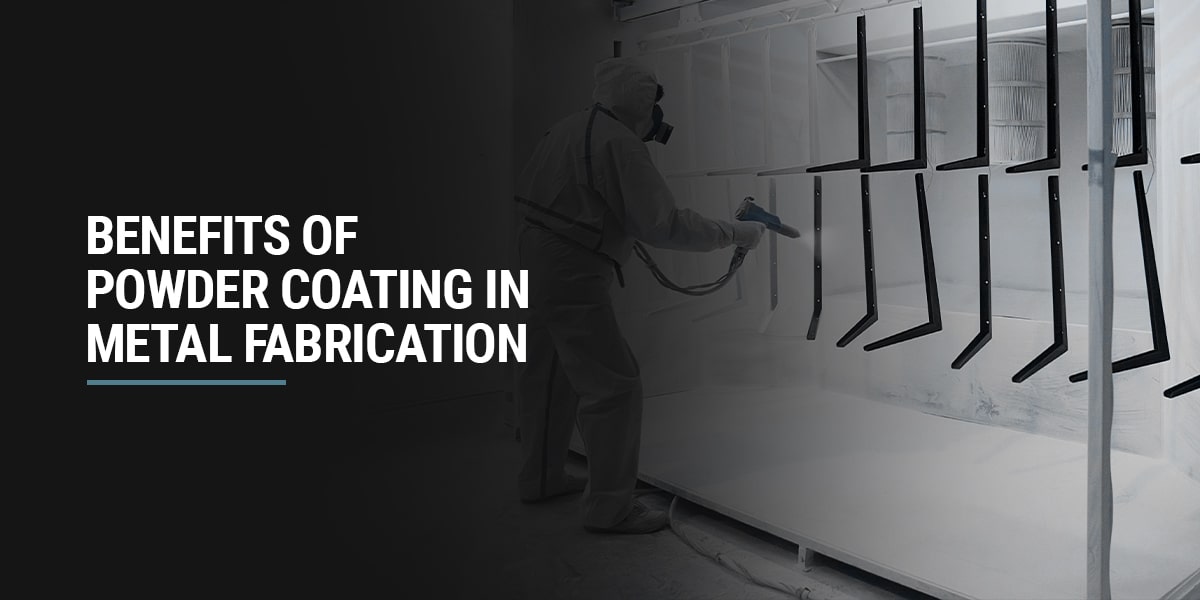
From heavy equipment manufacturing to consumer goods, there are seemingly endless applications for powder coatings on metal fabrication projects in various industries. Its popularity is easy to understand — powder coating is a high-quality, long-lasting finishing process that adds value and longevity to metal parts and products.
This post will explain what metal finishing is and why it’s important, how powder coating works and the great benefits of powder coating for metal products.
The Importance of Metal Finishing
Metal finishing is a catch-all term for several different processes. Metallic parts — also called substrates — are cleaned and coated with a top layer of metal, paint, powder or other material.
Metal finishing is an important step for many products because it:
- Minimizes wear and tear: Metal finishing eliminates microscopic scratches on metal surfaces, making parts more resistant to corrosion, friction and torque. As a result, finished parts last longer and require less maintenance than unfinished parts.
- Primes surfaces: Removing abrasions from metallic surfaces is an effective priming method, letting paint, powder and other coatings adhere better.
- Enhances aesthetic appeal: Finishing metallic surfaces creates a smooth, attractive appearance. Finished surfaces are also easier to clean than unfinished surfaces, making it easier to maintain the product’s appearance over time.
- Increases electrical conductivity: Substrates made of materials like stainless steel or titanium can receive a coating of nickel or copper to boost their conductivity, providing enhanced material flexibility for manufacturers.
How Do Powder Coatings Work?
Powder coating is a finishing process that covers a substrate with an electrostatically charged plastic powder and cures it to create a uniform seal. This process is known as a dry finishing process because the powder spray does not contain a liquid element. Powder coating protects the metal product from environmental damage and excessive wear.
What Is Powder Coating Made Of?
Typically, manufacturers will use two types of powder in this process:
- Thermoplastic powders: Thermoplastics melt when exposed to high temperatures. This property makes thermoplastic-coated products easy to repair — you only need to heat them and allow the coating to flow back together.
- Thermosetting powders: Thermosetting powders harden under high temperatures, creating a strong, permanent coating. They’re typically also a more cost-effective option than thermoplastics, making them an excellent choice for projects with lower budgets.
Common Powder Coating Uses
Common applications for powder-coated metals include:
- Heavy equipment: Heavy-duty equipment such as construction and agriculture machinery must withstand extreme conditions in typical operation. Powder-coated metal components are highly durable, making them excellent choices for this application.
- Automotive: The automotive industry utilizes powder coating for many different car parts, including hubcaps, truck beds, radiators and decorative accents. Many vehicle manufacturers also apply a clear powder topcoat for additional auto body protection.
- Consumer appliances: Many household appliances such as cooking ranges, washing machines and air conditioners have powder-coated panels to create a striking appearance and enhance machine longevity.
How to Cure Powder-Coated Products
The powder coating process is quicker and more efficient than other finishing processes. It produces significantly less waste and involves just three steps:
- Priming: Before applying the powder coating, you must first prep the surface with an abrasive method like sandblasting or vapor honing. This step creates a smooth, uniform surface, ensuring that the coating will stick to your product without leaving any gaps.
- Application: Once you’ve prepped the surface, you apply a positive electrostatic charge to a pigmented dry powder and spray it directly onto the negatively charged metal surface. The electric polarization promotes adhesion, completely coating the product.
- Curing: Finally, you cure the coating by baking the product in a specialized oven where the coating melts and gels together to create a smooth, unified surface.
Because powder coating is a dry finish, you don’t need to wait for it to dry and most products are ready for use immediately after curing.
The Benefits of Powder Coating Metal for Steel Fabrication
You can powder coat aluminum and most steel alloys — in fact, you can apply powder coating to any metal that can hold an electrostatic charge. There are many benefits of powder coating for steel fabrication projects because of its:
- Aesthetic appeal: Powder coating creates a smooth, uniform surface for your steel fabrication projects. It’s also highly customizable, with various surface finishes, colors and textures available to create your desired appearance.
- Durability: Powder coating protects steel products by creating a durable seal that reduces wear and tear and improves resistance to corrosion and rusting. As a result, powder-coated steel products are long-lasting, even with little maintenance.
- Low maintenance: Powder coating requires little maintenance to keep it looking good and working well. All you need to do is wash the product with regular soap and rinse it off with water as needed — no reapplication or special cleaning solutions are necessary.
The Advantages of Powder Coating vs. Alternatives
The advantages of choosing powder coating over other options include:
- Efficiency: The powder coating process is significantly quicker than other metal finishing processes because there’s no need to wait for layers to dry.
- Cost-effectiveness: Because the coating process is so efficient, it requires less time and labor, making it an excellent choice for keeping smaller projects within your specified budget.
- Lower environmental impact: Powder coating is free of harsh chemicals and solvents, making it safe for disposal. It also produces less waste than other finishing methods, so there is less material to dispose of at the end of the process.
- Versatility: Powder coating is suitable for use on any metal that can hold a negative charge and withstand high temperatures, including pieces of irregular shapes and sizes.
If you’re looking for an affordable finishing process you can use on various metal fabrication projects, powder coating is a great choice. Be sure to ask your manufacturer about their powder coating services before making a final decision.
Contact Superior Manufacturing Company for Powder-Coated Metal Finishing
At Superior Manufacturing, we pride ourselves on providing our customers with the highest-quality metal parts and products. When you work with us, you have ultimate control — we work to your unique specifications, creating highly customized products to meet your application’s specific requirements. We also complete every project in-house, so when you choose to partner with us, you can do so with confidence.
We offer several finishing options, including powder coating. Our automated paint system efficiently applies powder and liquid finishes, allowing us to provide a quick turnaround without sacrificing quality.
Contact us today to request a free quote or to learn more about our manufacturing capabilities and custom engineering services. We look forward to working with you.