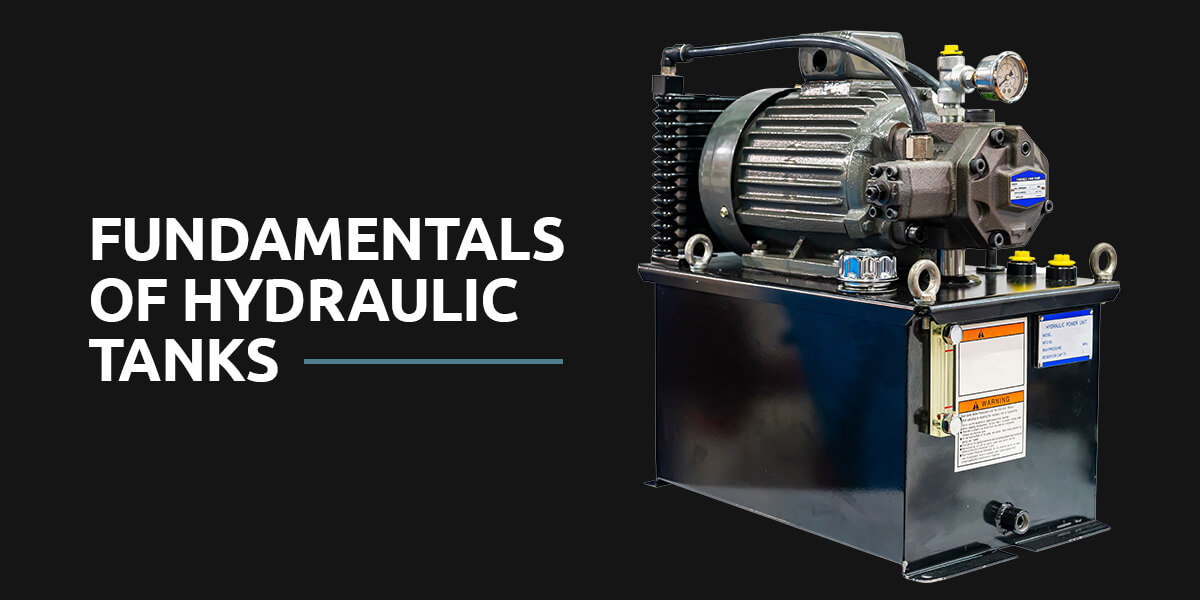
Hydraulic systems rely on large volumes of hydraulic fluid to operate adequately, especially in heavy-duty applications such as construction equipment, heavy machinery or industrial spaces. Hydraulic tanks are an essential part of hydraulic systems, storing and managing the necessary hydraulic fluid so the equipment or machinery can use it effectively and function efficiently. Learn the fundamentals of hydraulic fluid tanks and why they’re a critical part of the hydraulic system as a whole.
What Are Hydraulic Tanks?
Hydraulic tanks, also called hydraulic reservoirs, are a vital aspect of hydraulic systems. Their primary purpose is to hold excess hydraulic fluid as the system’s oil volume changes and pumps in and out of the hydraulic cylinder. Since hydraulic tanks help regulate fluid levels, they’re most often used in applications where the fluid level fluctuates, like in agricultural, material handling and industrial applications.
In addition to holding a reserve of hydraulic fluid, these tanks play several other crucial roles in hydraulic operations. For example, a hydraulic tank helps cool and aerate the hydraulic fluid and prevents contaminants from circulating through the system by providing space for them to settle in the bottom of the tank. Hydraulic tanks also vent air in and out of the tank as it separates from the fluid.
Depending on the size of the tank, they can also often serve as a mounting surface for several other system components, including electrical control panels, the motor, hydraulic pump assemblies, filters and accumulators.
How Does a Hydraulic Tank Function?
Hydraulic tanks or reservoirs connect directly to the system’s hydraulic cylinder through a pipe or line. Hydraulic fluid moves through this line from the tank into the hydraulic cylinder as it extends and back into the tank as the cylinder retracts.
To allow this circuit to flow smoothly, a breather at the top of the tank allows air to come in and out as the fluid levels fluctuate. This air movement prevents too much pressure from building up and allows the fluid to expand or compress as the temperature changes. Additionally, baffles or partitions inside the tank help circulate the fluid more thoroughly as it returns to the tank. This process helps cool the fluid, separate air from the fluid and settle contaminants at the bottom of the tank.
While the basics are generally the same in most tanks, hydraulic tank functions can vary depending on the type of tank used. Hydraulic tanks are typically categorized into two types:
- Atmospheric tanks: Atmospheric tanks use open atmosphere breathers, which means the pipe or line that transfers fluid into the cylinder depends on air entering the tank passively to help push fluid into the cylinder. The atmospheric pressure and liquid level combined create the total pressure necessary to complete the cycle, and you cannot manually adjust the pressure on this type of tank.
- Pressurized tanks: To maintain a specified pressure, pressurized tanks rely on an external air tank that feeds pressurized air into the hydraulic reservoir. A regulator monitors the tank’s pressure and controls when pressure is released and when air is added to the tank. These tanks allow more control over the pressure within the tank.
What Are Hydraulic Tanks Made Of?
Hydraulic tanks can be made from several different materials, each offering different benefits depending on your application or system’s needs. Most tanks are made from metal, though they can also be plastic. Here are the four most common materials used to make hydraulic tanks:
- Steel: Steel is a popular material choice for hydraulic reservoirs because it’s relatively cost-effective, easy to work with and readily available. Steel is an effective heat dissipator, which helps regulate the hydraulic fluid temperature. However, this material is heavy and prone to rust without proper cleaning and care.
- Stainless steel: Although it costs more than standard steel, stainless steel is often preferred because of its durability and corrosion-resistant properties. Stainless steel is treated to prevent rust and improve the material’s life span. Like standard steel, stainless steel also dissipates heat effectively but offers a sleeker appearance and requires less maintenance.
- Aluminum: Aluminum is another popular hydraulic reservoir material for its excellent heat dissipation. While it’s highly resistant to corrosion and one of the most attractive materials, aluminum is also generally more expensive and relatively fragile compared to other options. Despite these drawbacks, aluminum can be an effective material for hydraulic tanks with the right fabricator and system setup.
- Polyethylene: Some people prefer to use polyethylene plastic to manufacture hydraulic reservoir tanks because the material is lightweight and much less susceptible to condensation than metal. However, polyethylene is a poor heat dissipator and should only be used for short-duty cycles to prevent overheating.
Hydraulic Tank Sizing
The size of a system’s hydraulic reservoir is crucial to the success of the entire hydraulic system. It’s best to leave tank sizing to a professional manufacturer who can calculate the appropriate size based on the system’s heat balance and how much heat needs to be dissipated through the hydraulic tank. Since every hydraulic system has different reservoir sizing needs, having a professional hydraulic tank manufacturer measure your system’s unique requirements is the best way to ensure you have an appropriately sized tank.
In most cases, it’s best to size up when you can to ensure your hydraulic reservoir is large enough to accommodate fluctuating fluid levels and thermal expansion as fluid sits in the tank. Generally, most reservoirs should hold at least twice the pump output.
What Are the Benefits of Hydraulic Tanks?
One of the biggest benefits of having a hydraulic reservoir is that it serves multiple functions. From simply holding excess fluid to regulating and conditioning the fluid, hydraulic reservoirs are an advantage to any hydraulic system. Here are a few other benefits of having a hydraulic tank:
- Manage heat generation: Hydraulic fluid coming into the tank is generally hot and contaminated, meaning it shouldn’t cycle directly back into the system. A reservoir holding excess fluid allows the returning fluid more time to cool down before returning to the system.
- Simplify system configuration: You can mount many essential parts of a hydraulic system on the reservoir. With this designated area for configuring system components, you’ll benefit from a simplified and centralized design.
- Reduce contamination: In addition to managing heat generation, hydraulic reservoirs prevent contaminants from recirculating and damaging the entire system. Hydraulic tanks allow any contaminants to settle at the bottom of the tank and can also feature filters to reduce contamination even more effectively.
- Release air: A hydraulic reservoir allows air to separate from the hydraulic fluid and escape through the breather at the top of the tank. Releasing air from the system protects it since air in the system could cause severe damage.
Get a Custom Hydraulic Tank From Superior Manufacturing Company
Hydraulic tanks don’t have a one-size-fits-all solution. At Superior Manufacturing Company, we create custom hydraulic tanks for OEMs and other heavy-duty manufacturers. With over 75 years in business, we have the expertise to make high-quality metal hydraulic tanks that meet your specifications and equipment requirements. We handle every aspect of production, from fabrication and painting to assembly and quality control.
Contact us to learn more about our process and get a quote today.