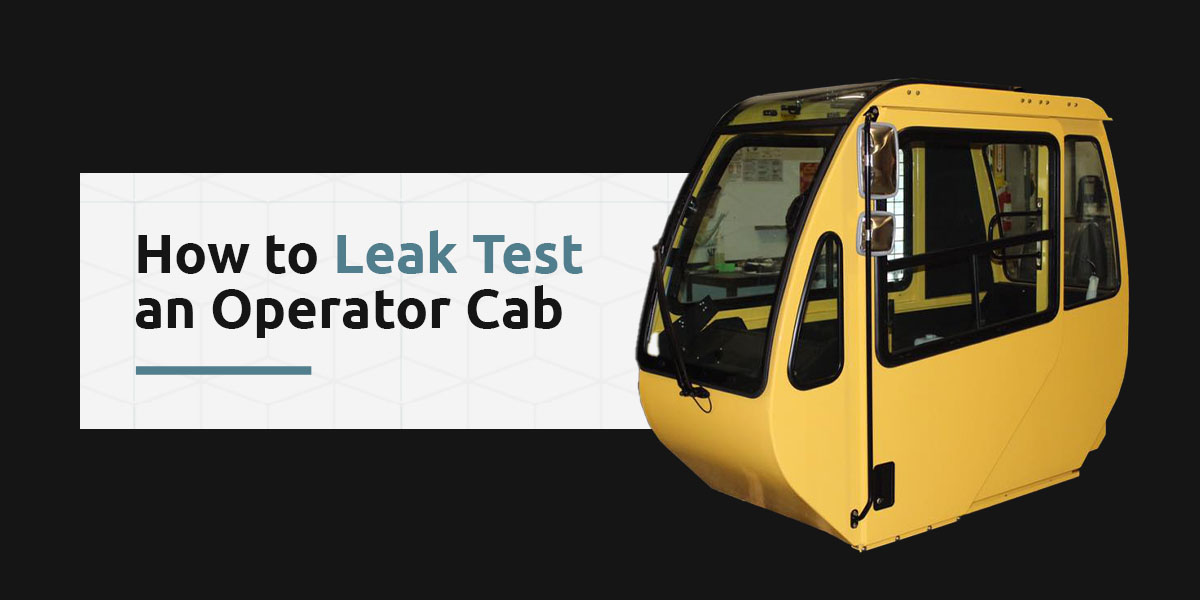
Heavy equipment operators already work in a dangerous environment, and a leaking operator cab doesn’t do them any favors. For businesses, leaks can also mean violating workplace standards and subsequent fines. Manufacturers must test cabs carefully after production, and users must continue periodic testing during use to ensure operators stay safe while using the equipment.
Still, that job can be complex. Leak tests can come in many forms, and different industries may have different standards or tolerances to meet. Knowing how to leak test an operator cab is a critical part of maintaining safety and dependability in any environment.
What Is a Leak Test?
Technicians can perform leak tests in many ways, but the overall goal is to identify the presence and characteristics of leaks, whether they be from liquids, gasses or particles. Different parts and pieces of equipment will call for various methods of leak tests. You might test pipes, hermetically sealed enclosures, cabs and many other components to look for worn seals, punctures, cracks, corrosion and any problem that could lead substances to go where they shouldn’t.
Leaks often occur when a substance moves from a high-pressure space into a lower-pressure space, but they can also occur from more random movements, like silica dust floating around a mining site.
Leak testing usually involves finding:
- The presence of a leak
- The size of the leak
- The speed of leakage
- The substance being released
Why Is It Important to Conduct a Leak Test on an Operator Cab?
Some leaks are less troublesome than others, like a puncture in the line of compressed air equipment that only causes efficiency problems. Others are incredibly hazardous to human health and safety. If a leak causes toxic substances to enter the air or creates a flammable environment, for instance, finding and fixing it is crucial. Operator cabs usually fall under the latter category.
An operator cab is a protective structure that keeps operators safe from visible threats like falling objects and hard-to-spot threats like chemicals and dust. Workers have the right to safety, which is why organizations like the National Institute for Occupational Safety and Health (NIOSH) have established strict standards for leaks. Other organizations, such as the American Society for Testing and Materials (ASTM) and the International Organization for Standardization (ISO), have also created guidance about testing methods and allowable tolerances. Many codes and inspections rely on these standards.
Some things businesses look to achieve with leak tests include the following:
- High operator safety and comfort: Again, keeping operators safe and healthy is a significant motivator for leak testing. From a business perspective, leak-free cabs help operators stay energized, alert and comfortable while operating equipment and reduces the costs of occupational health claims.
- Better compliance: Ensuring your operator cab meets appropriate standards can help keep businesses and products in compliance, which also helps avoid the costs and reputational damage associated with penalties.
- Equipment longevity: Cab leaks can cause damage to sensitive components inside the equipment. If the leak is coming from an internal component of the equipment, it could cause more serious problems for the vehicle. Testing for leaks can help ensure the equipment lasts as long as possible.
Common Leak Test Methods
You’ll find many types of leak tests available, chosen based on factors like the material involved and the type of equipment being tested. Since leak testing operator cabs often occurs in the field or right off an assembly line, most leak tests are non-destructive methods.
Some common methods of leak testing include:
- Bubble tests: Water-immersion bubble tests are some of the simplest methods of leak testing. These tests involve dunking a charged or pressurized part underwater and seeing if and where bubbles escape. Larger bubbles indicate larger leaks. Technicians can also perform soap solution bubble tests by spraying a soap solution onto a part. Bubbles would form if a leak were present. The bubble test option is usually best if the technician suspects a leak.
- Pressure and vacuum decay tests: A pressure decay test adds high-pressure gas to the closed system before isolating it from the gas supply. After a period of stabilization, the technician monitors the internal pressure to assess whether the pressure drops and how quickly it drops, which indicates the size of the leak. A vacuum decay test goes in the opposite direction, evaluating how quickly the pressure increases in a low-pressure system.
- Tracer gas detectors: Tracer testing involves detecting and measuring the movement of a tracer gas, such as halogen gas, helium or a nitrogen-hydrogen mixture. These substances typically do not interact with the substance in the system and pose little to no environmental burden.
Leak Testing Considerations
Keep these factors in mind before conducting leak tests and when interpreting results:
- Applicable standards: Of course, you’ll need to know the precise demands of any applicable standards or requirements. Some may, for instance, demand very precise measurements. Know your acceptable leak rates and choose testing mechanisms accordingly.
- Component characteristics: Not all testing methods will work with all products. You cannot use a bubble test to submerge an entire operator cab, but you can submerge small components. Some materials will also call for specific methods. For instance, you can’t perform a vacuum decay test on a part with thin walls that can’t withstand external pressure.
- Leaking chemicals: Some substances behave in unique ways. You’ll need to consider the characteristics of the substance you’re looking for, such as the molecule size and the effects of temperature. You must also determine how much pressure is needed for a leak test.
- Speed and accuracy: Testing methods used in production lines typically need to be fast while meeting accuracy requirements. When choosing a method, you’ll also need to consider how long a leak test takes on a cab. Some strategies work well in assembly lines, while others work best in the field.
Meet Leak-Testing Requirements With Quality Equipment
An uneventful leak test relies on high-quality equipment and assembly. At Superior Manufacturing Company, we know how important leak testing is and what it means for your products. We put over 75 years of engineering expertise to work to deliver fabricated metal products, like operator cabs, that meet precise demands for leak-free performance.
If you need to implement leak testing for operator cabs or are looking to change your system verification processes, our knowledgeable team can help. Reach out to us today to learn more about leak tests for operator cabs and how Superior Manufacturing provides components that pass the test.